top of page
EMPowered Heat
RF XL 2.0 for Heavy Oil

Our goal is to economically produce more oil faster while providing the capability to virtually eliminate Scope 1 and almost all Scope 2 GHG emissions.
RF XL 2.0 is an enhanced EOR technology that uses RF heating to energize oil formations. It is a major innovation that could potentially decarbonize heavy oil and oil sands production effectively and efficiently, materially lowering costs compared to other EOR techniques, and increasing the recovery factor.
RF XL 2.0 builds on the RF XL Marwayne deployment, which successfully demonstrated RF XL’s potential by heating the reservoir and increasing temperatures in the production well while achieving the highest power level and longest continuous run time for any RF based EOR technology.
Lowest Cost
Lower Capital Cost
50%
Utilizing Acceleware’s RF XL 2.0 technology in place of SAGD is estimated to reduce the capital costs of oil sands and heavy oil production by over 50% on both a capital intensity (dollar per flowing barrel) and a total capital investment basis.
With minimal surface facility requirements and the mobility of the CTI, RF XL can be deployed at a single well or a single pad, allowing operators to profitably scale one well (or pad) at a time and relocate the system multiple times to optimize productivity and returns. The reduced size, scale and ability to redeploy the RF XL system deliver faster return on investment and higher profitability.


Lower Operating Cost
40%
RF XL operating costs are driven down by an estimated 40% by a combination of decreased energy input joule for joule versus fossil-fuel based heat and versus other forms of electrification, labour and service costs. RF XL requires no ticketed steam engineers, no steam based pressure vessels, and reduced pressure vessel compliance work.
The simplified surface operations of an RF XL deployment would require fewer staff to operate, have lower maintenance and workover needs, and require less water processing and disposal. RF XL is remotely monitored and managed, so staff are only dispatched as needed for maintenance or repairs.
RF XL Commercial Scale Demonstration
RF XL 2.0 builds on the RF XL Marwayne deployment, which successfully demonstrated RF XL’s potential by heating the reservoir and increasing temperatures in the production well while achieving the highest power level and longest continuous run time for any RF based EOR technology.
Construction of the commercial-scale RF XL pilot was started in August, 2021 at Marwayne, Alberta. The CAD $30 million pilot saw seven consecutive months of EM power injection into the transmission lines, proving out the core heating technology and the Clean Tech Inverter (CTI).
The commercial-scale pilot is intended to demonstrate RF XL’s heating capabilities, alongside immediate and sustainable environmental, economic and social benefits. These include 40% operating cost and 50% capital cost reductions, no external water use requirements, near-zero GHG emissions through direct or indirect use of renewable power, a significant reduction in surface disturbance and no requirements for the addition of solvents.

RF XL technology could enable production from a wide range of untapped geologies and reservoir formations, including:
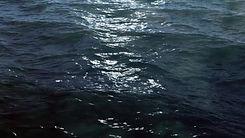
Very deep or very thin reservoirs

Cracked or fractured rock

Shallow reservoirs
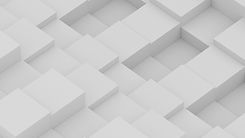
Developed reservoirs with up to 90% of the oil still in the ground
How RF XL Works
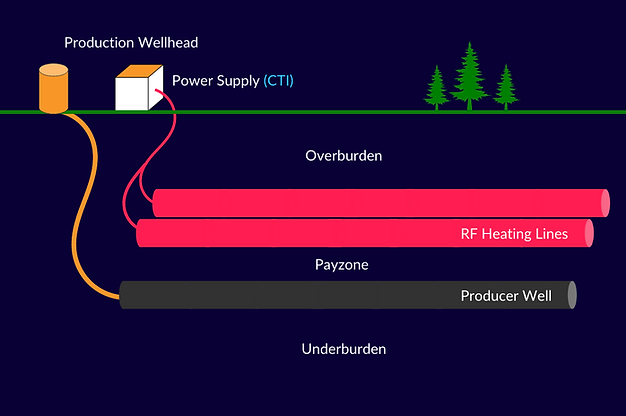
RF XL uses RF energy to generate heat, which converts the water already existing within the oil sands reservoir to steam, mobilizing the bitumen and allowing it to flow to the producing well.
Acceleware's RF XL process, coupled with new software advancements, involves the drilling of two RF heating lines into the target zone and their connection to a surface power supply.
RF XL eliminates the need for water source wells, water treatment equipment, and steam generators, as well as the requirement for costly chemicals or solvents.

bottom of page